Today I got the end nose rib notched and the wingtip glued in place. I have the blocking at the spar tips and nose rib, but will still need to block and shape the trailing edge as well as gluing in the plywood gussets. Still, it feels good to have the wingtip on. It looks more like a wing!
I also trimmed the CW36 pieces. These go on the ribs just outside the aileron bay and hold the torque tube support bushings. As supplied they were about 3/8 too long for the inboard side, and 7/16 for the outboard side where there’s an additional thickness of plywood where the wingtip spar web overlaps. For this I just set the miter gauge on the table saw to match the angle of the piece, then set the table saw to cut off the length needed. I won’t glue those two pieces in place until after I have the rest of the aileron structure built up.
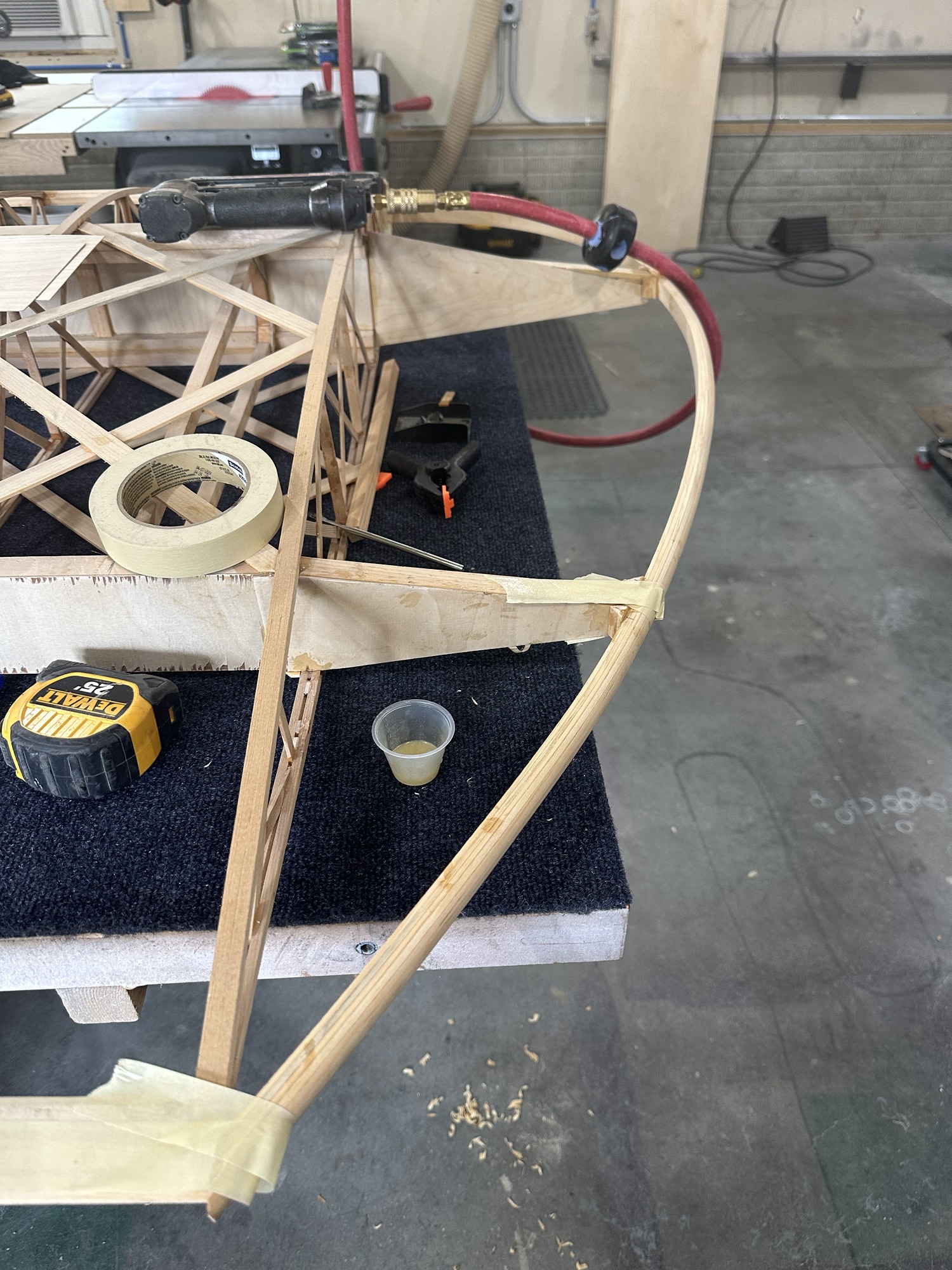
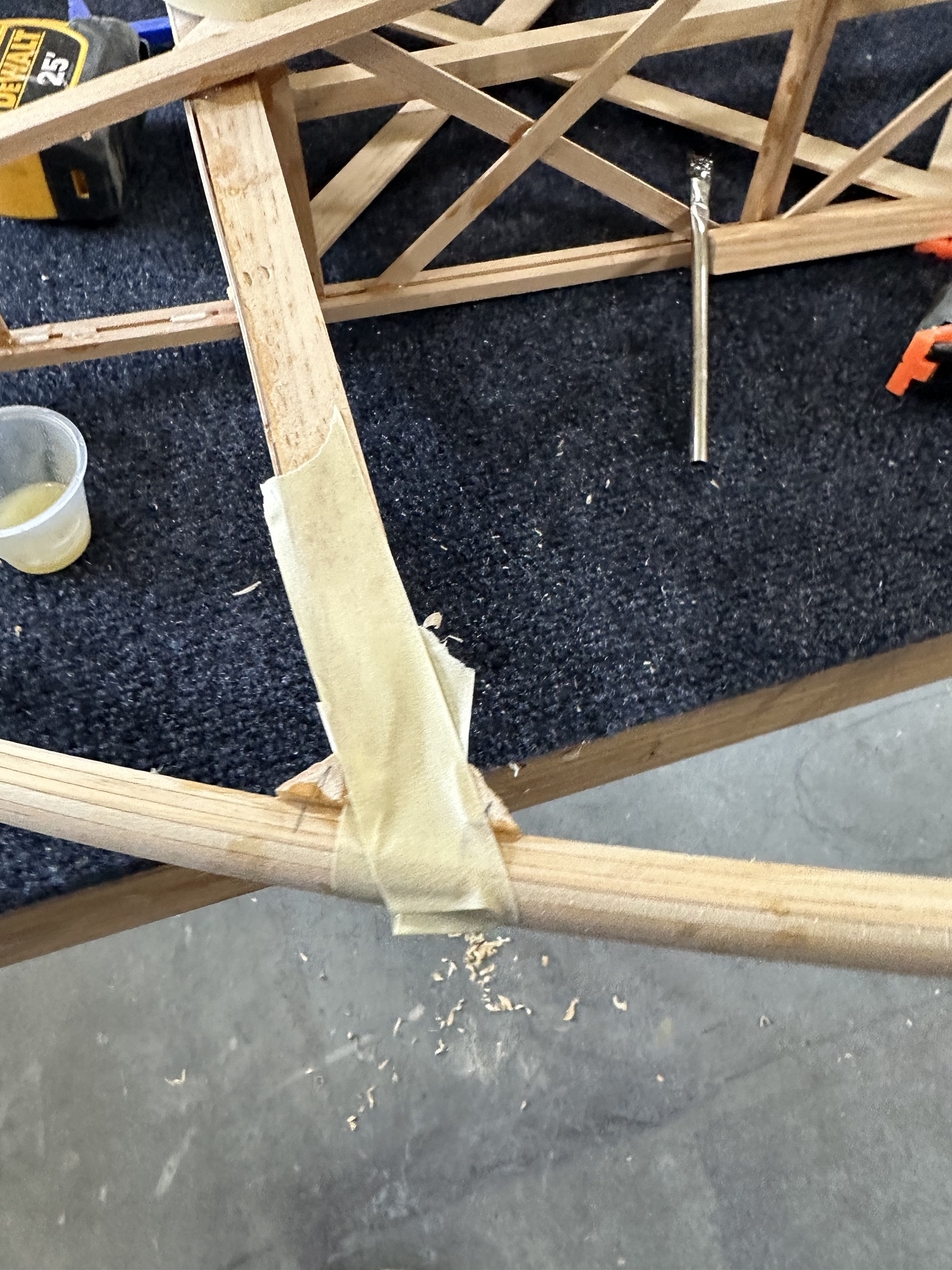
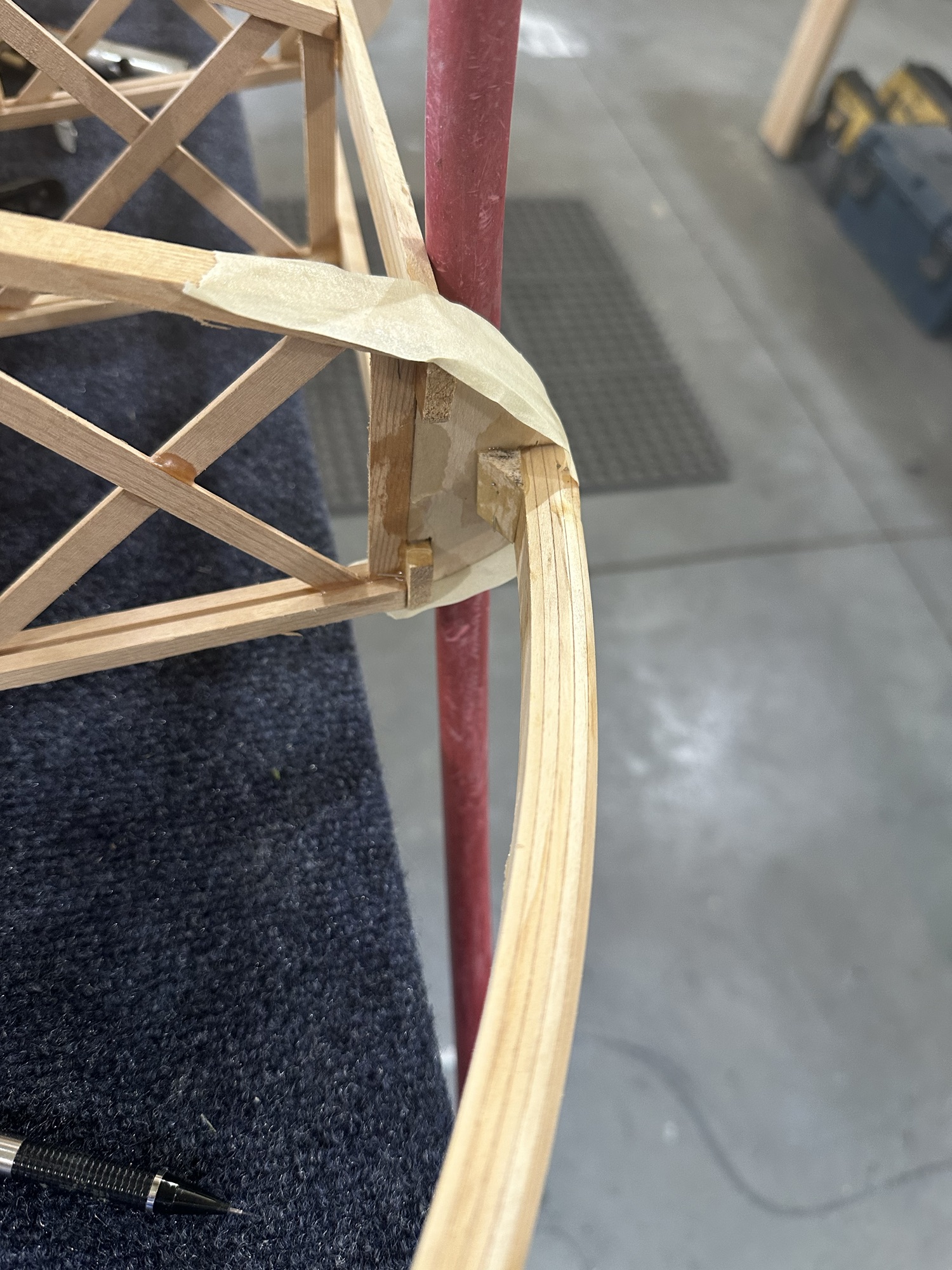