This morning I went over to check on the work I did yesterday. The main portion of the walk structure looks good. I still needed to get the extension (front portion) ready for the skin.
The center plywood support is glued to the first false rib, but of course the plywood skin sits between the ribs. That meant I needed to shave about 1/8″ from the top cap of the false rib. I used the razor plane for most of this work but needed to use a file for some of it like the front edge. I cut the cross supports and used them to gauge whether the top of the middle support/rib was level with the other two. In the end I used a DA sander to “fine tune” the high spots until it was all level.
I also wanted to make sure the front and back edges of the thin plywood are fully supported and level with the thicker ply on the rear portion of the walk. I ended up just cutting a couple of support strips to attach to the top of the spar; I use da cutoff scrap of the wing walk for this as it was the perfect thickness. I also cut a couple of pieces of rib capstrip (I’ve got a lot of it left) to glue to the false spar to support the front edge of the walk extension. The plans don’t call for it, but I’ll feel better with a little added structure there.
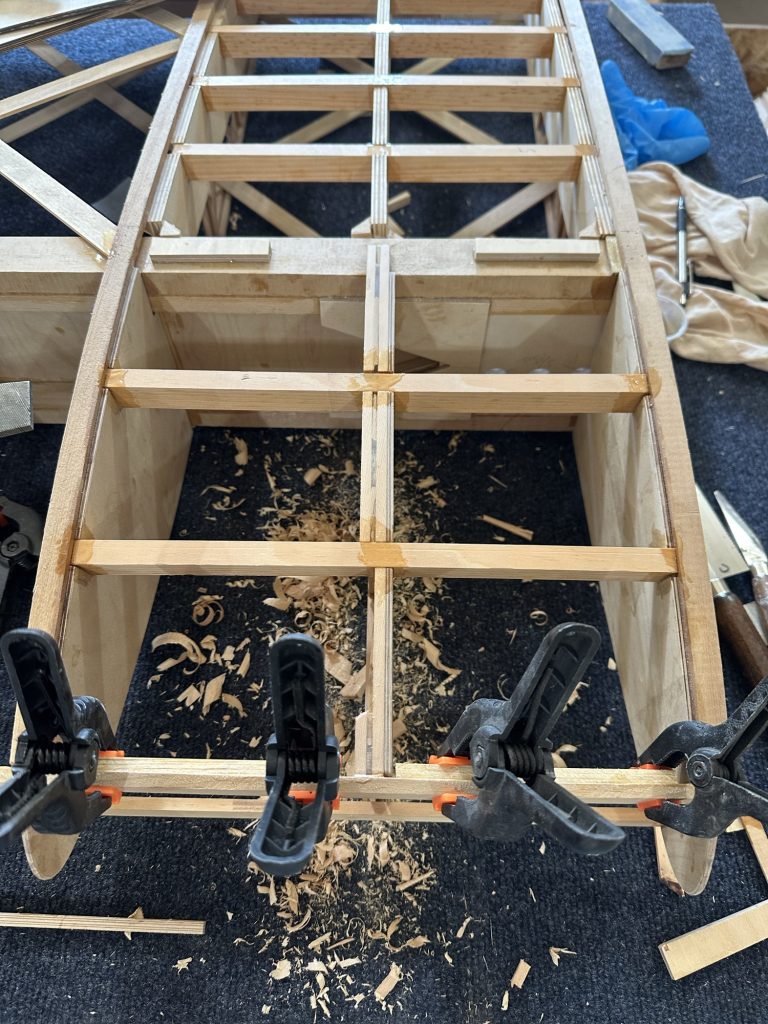
The plans call for using nailing strips and brads to nail down the plywood skins while the glue dries. That’s one way, but I’m thinking another way would be longer clamping strips and long clamps. One strip would hold down the aft end of the main walk and get clamped to the rear spar. One would hold both the forward end of the main walk and the aft end of the extension and get clamped to the main spar. A third would hold down the forward end of the extension… I’m not entirely sure how that one would get clamped, but since it’s 1/8″ plywood it won’t need a lot of clamping force. I’ll find a place, I’m sure.