After a couple days’ hiatus for Thanksgiving, I went over yesterday to resume work on the wing. We cut the notches in the nose ribs and got them glued in place, and I cut and glued the corner blocking for the four compression struts. I still need to cut and glue in the gussets for those. We took a look at some of the aileron pieces to figure out how all of that goes together. I’m waiting on a response from Millard Metals on my aileron torque tube stock; I don’t think we can do much until I have that. I think the next step will be to get the wingtip bow figured out, and wrap the leading edge with plywood. Then I could also start cutting and installing the bushings for all of the attachment bolts.
Lower left wing, Day 4
Last night I got the compression struts and the bottom geodetic bracing glued in. Next up will be gluing the various plywood pieces surrounding and supporting the ailerons. I got those out last night to see how they fit, and everything looks good so far. Waiting to hear back from the metal supplier on the 1″ diameter tubing I need for the ailerons.
Lower left wing, Day 3
Last night I attached the two false spars to the nose of the ribs, and got the vertical blocks for the compression struts glued to the front and rear spars. The next step will be to flip the wing over and finish off the compression struts. Lots of pieces to those; it’s really the first place where I’ll need to install corner blocking and gussets. I know, most wood airplane builders would have been doing that all along!
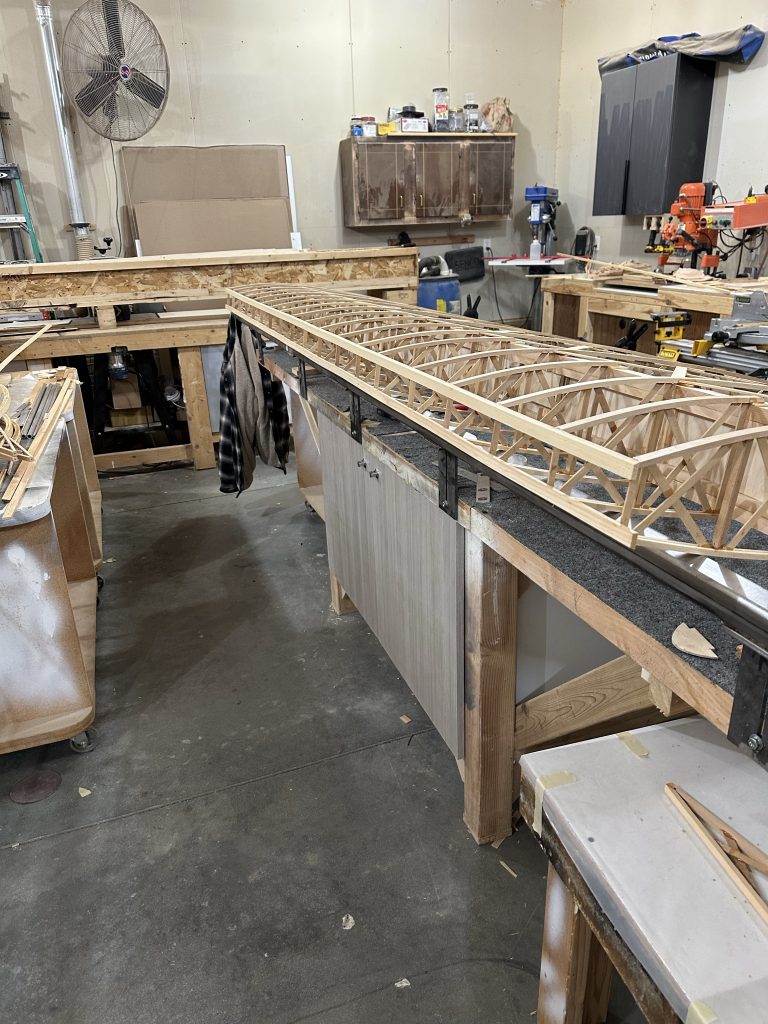
Lower left wing, Day 2
I feel like we accomplished a lot today. This morning Stu and I unclamped the partially assembled wing and found that it was already quite stiff and of course perfectly square. The epoxy where the ribs were glued to the trailing edge material was pretty well stuck to the steel rail, but the careful use of a utility knife blade between wood and steel popped those spots loose. Next time we’ll use poly or waxed paper. Stu sanded the rail to remove the epoxy and applied a couple coats of paste wax.
We stood the wing panel on its nose and slid the main spar into place, then glued and pinned the ribs to the bottom of the spar. The first rib was placed flush with the end of the spar, and the rese were once again set in place using the 11.5″ gauge block that we’d used for the rear spar rib spacing. It perfectly matches the notch spacing on the trailing edge, so everything remains perfectly spaced and square. Once that was done, we rotated it back horizontal and re-clamped the trailing edge to the rail. Now I cut some short lengths of laminating strip material to act as shims between the spar cap and rib caps, so we glued and pinned the ribs to the top rib cap.
With that done, we glued the false ribs in place using a 5.5″ gauge block. Lile the main ribs, these were glued and pinned to the bottom of the spar, then shimmed, glued, and pinned to the top.
As I had some glue left over, I decided to attack the geodetic bracing. I hadn’t really intended to do it all, but in the end all of the top surface geodetic braces are glued and clamped in place. We’ll do the bottom surface after the compression struts are done. What remains is the compression struts, bottom geodetics, nose ribs and plywood, and ailerons. And that’s where it’s all going to get messy. When I modified the ribs to clear the rear spars in the upper wings, I inadvertently put the cross braces right where the aileron torque tubes need to go. Oops. Not a problem on the upper wing, but it is on the lower wing. I think my fix for this will be to simply remove the pair if X braces (that I just installed) on the non-aileron ribs, and glue on a side plate cut from 1/16 plywood to stiffen that part of the rib. Then I can just have a hole for the torque tube. This should make the rear portion of those ribs substantially stronger than using the geodetic bracing, and will be only very slightly heavier. The upper wings should not need this modification, only the lower wings.
The last two wingtip bows came off the forms and are ready to install, so we removed all the screws from the table and stacked them until it’s time to finish them off. We’ll likely sand the top and bottom surfaces to remove the excess epoxy, then run the outer edges through the router table for a 3/8 radius top and bottom.
Lower left wing assembly
I chose the lower left wing to start with since it is the simplest of the four. The lower right will get the wing walk, and the upper wings get a diagonal cut on the inboard bay.
This morning I pulled the first two wingtip bows from the forms; they look pretty good. I mixed up about 40cc of glue and started gluing up all of the strips for the second pair of bows. Had to mix another 10cc, so if I ever do this again I know it takes 50cc per pair of layups. I got them clamped into the forms and slid the table as far out of the way as possible.
The plans say to nail or screw a block of wood to the top of the bench, square with the trailing edge to set up the wing. Since we’re not building it resting on the bench, Stu and I squared up the first rib with the TE (which is clamped to a steel rail) and marked & clamped it to the other rail. After some debate, we decided to pull the main spar out temporarily. I needed to pull the TE of the rib from the notched TE stock to glue it, and with both spars in place it was nearly impossible to do so. The rear spar is a pretty snug fit in the ribs, but the main has about 1/8″ of clearance so it’s relatively easy to slide out and back in.
Rather than a continuous piece of trailing edge material long enough to do a complete wing, this kit had four 8′ long pieces and four pieces roughly 4-1/2′ long, I cut the longer piece just inboard of the first aileron rib, and started one of the shorter pieces at that point. We got them aligned and clamped well enough that you can’t tell where the joint is if you sight down the trailing edge.
Stu cut a rectangular block about 6″ tall by 11-1/2″ wide, since that’s the distance in between each pair of ribs. With the first rib glued in and squared to the TE, it was then just a matter of using that gauge block to seat each rib exactly where it needed to be on the rear spar. Each rib was glued to the TE and rear spar, and a couple of 1″ micro pins shot through the rib cap to hold it in place while the glue cures. Working that way we got the entire set of ribs in place. We’ll let the glue cure and slide the main spar back in place tomorrow, glue the ribs to it, and attach the false ribs
I did some other work today, including trimming the false ribs so they’re ready to install.
Building the Wingtip Bows – and more
It’s really nice working in Stu’s shop with lots of room and plenty of work surfaces. One of those work surfaces is a 48″ square low table, with a 3/4″ melamine laminate top. It’s just the size needed for laying out thew wingtip bows. I started out by laying a large piece of cardboard out and taping the plans page over it. Then I used a sharp punch to poke through each of the nail locations on the plans to mark on the cardboard where they should be. Since I wanted to get two bows done at a time, I then rotated the plans page and marked a second set of nail locations.
Rather than hammer nails into the tabletop, we taped some poly sheet and then the cardboard down onto the surface and drilled 1/16 pilot holes. Stu has a bunch of trim head screws, so we sunk those using a block of wood as a depth gauge so that the heads are just above the 3/4″ mark – since we’re laying down 3/4″ lamination strips. With all the screws in place we pulled off the cardboard, leaving the poly sheet and screws.
Knowing that I’d need to spread a lot of epoxy in a short amount of time, I bought a small silicone glue roller and tray. The tray is about 6″ long by 3″ wide, and the roller is a bit under 2″ wide and is grooved to hold more glue. Since it’s all silicone rubber, the cured epoxy just pops right off after use.
After getting all the screws in place, I wanted to see whether I would need to soak the wood laminating strips to get around the form. I had no trouble whatsoever getting the strips bent around the forms without any soaking, so that was good news. With that bit done, we trimmed 20 of the laminating strips (4 wingtip bows, 5 layers each) down to the right length to clamp down to the forms with a few extra inches on each end. With that done I went home for the night.
Friday morning I was back at it. Mixed up some epoxy in the silicone tray and used the roller to evenly coat 4 of the 5 laminating strips with glue. It worked wonderfully well, I’m glad I bought it. I then just stacked the strips and clamped them to the first form, then repeated the process with the second set of strips. The entire process was so much less complicated than I anticipated — I’m not the least bit worried about repeating it for the other two bows, or for the tail. Of course we’ll see how those bows come off the forms tomorrow…
With the bows curing, Stu and I drilled the holes for the bolts and bushings that will attach all of the fittings to the wing spars. Stu’s got a set of Forstner bits, which cut nice clean holes. I’ve got to get a set of those… been meaning to anyway, but that really drove the point home, so to speak. One big advantage is that with the drill press running, you can clearly see the point on the bit to precisely put it right on the mark. Then we cut the 3 degree angle on the lower wing main spar root ends. No pressure at all, just taking a chop saw to a nearly irreplaceable bit of very expensive spruce and aircraft plywood…
Now it’s time to start actually assembling the wings. We started by attaching a steel rail to the side of the bench to support the leading edge of the ribs. The idea is, rather than supporting the trailing edge material with an angled block to let the ribs sit on the bench tom, we’ll clamp the TE flat to one bar, then use the other to support the leading edge at the proper height to match the angle of the TE. If you’re building one of these, I wouldn’t recommend trying to do it this way without a similar setup. Stu’s got a pair of 12′ long square steel tube rails that bolt to the edges of the bench and can move up or down from slightly above the level of the bench top to about 5-6 inches high. It’s pretty unique. The method outlined in the plans is a solid alternative, though personally if I had to do it without this setup I’d bevel the edge of a long block and use pocket screws to attach it to the bench.
We got the first half dozen ribs in place but were unable to go further, since I had taken all of the aileron ribs back home — I just grabbed the stack of ribs that needed modification, and it didn’t occur to me that the aileron ribs could stay.
So that was today — a lot of progress. By the end of the day tomorrow we should have something that starts to look like an airplane wing, and two more laminated wingtip bows.
Rib modifications
I built all of the wing ribs exactly to plans, per Sheet 1 of the plan set. Unfortunately, that sheet has not been updated since the rear spar was changed from using 1/2″ square spar caps to 3/4″. As a result, the X braces just aft of the rear spar were way too far forward in all of the ribs I built — all except for the 16 aileron ribs, which don’t get those X braces. Installing the rear spar would require extensive trimming or notching of the geodetic stock — I just wasn’t happy with that. Plus, there’s another piece of square stock on the aft face of the rear spars on the upper wings. It already needs to be beveled to clear the ribs, and with the braces in place would need to be cut down to almost nothing.
So, out came the razor saw. I cut those two X braces from every one of the ribs, cut new ones, and glued them in place with enough clearance for the rear spar. It was a couple hours’ work, but since I have a lot of extra rib geodetic material wasn’t that big of a deal. On the bright side, I got to test the glue joints on all of the pieces I pulled out. We want the wood to fail before the glue does. Every single one of them broke the brace or separated it along a grain line before the glue gave up — 100% successful tests. That was not unexpected, but was reassuring nonetheless.
Now we can move forward with assembling the wings.
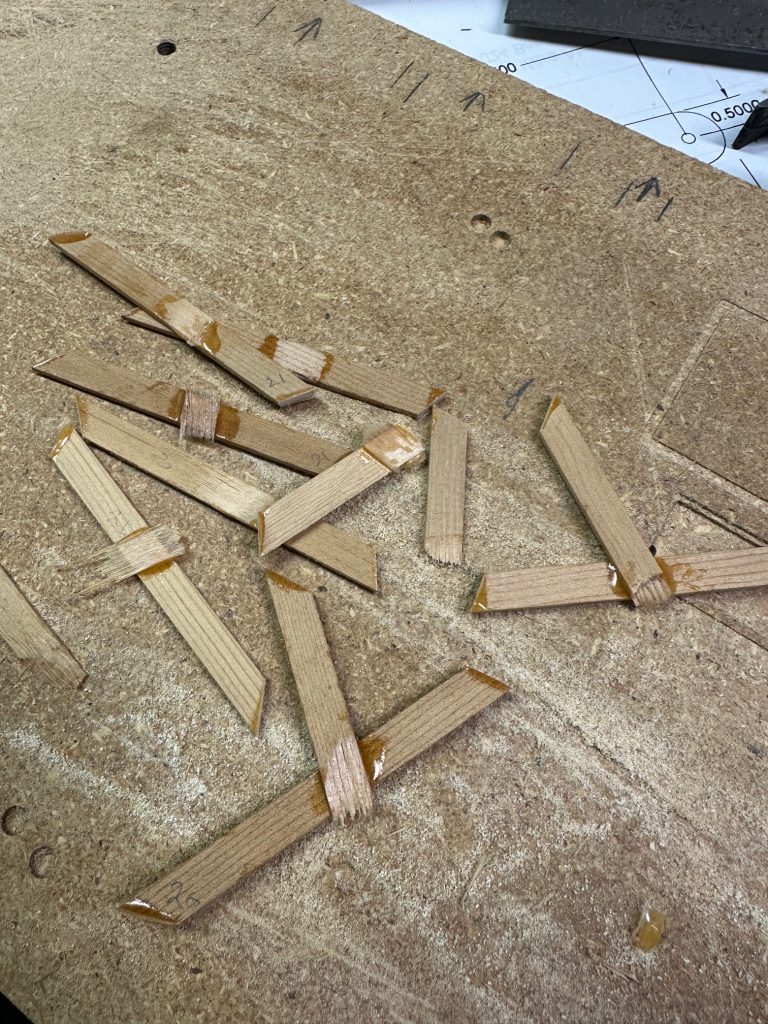
11/11 update
How many mistakes can one man make? Enough… thank God I’m building this out of wood, so things can be fixed!
With enough of the aluminum bits cut and drilled to get the spars drilled, I started laying out the hole locations for drilling. Along the way I found a couple of places where I’d gotten blocking in the wrong places for various reasons. Fortunately, in each case I was able to simply add some well fitted wood blocks to get the support where it’s needed. So far I figure the plane will be about two ounces heavier for the extra wood and epoxy. I can live with that. Still, it’s caused a bit of angst.
As of this morning, the next step is to cut the slight angle on root ends of the lower wing spars, drill the holes for all of the bolts, then start actually assembling a wing. At last.
First Aluminum
Today I picked up some flat bar stock from Millard Metals. The Celebrity wings use fittings of various sizes to attach flying wires, landing wires, N struts, and of course to attach the wings to the fuselage. These are made from 1/8″ and 3/16″ 6061-T6 and 3/16″ 2024-T4. I ordered some 6061 tubing from Aircraft Spruce to use as bushing stock. It will take me a while to get all of the brackets cut and drilled, but I did cut at least one of each piece and marked them for the bolt holes. I’ll drill them with small pilot holes, and once they’re all ready I can start drilling the spars for the bolts to attach them. Once those holes are drilled we can start assembling the first wing. I can install the bushings after the wing is assembled, but the holes need to be drilled first.
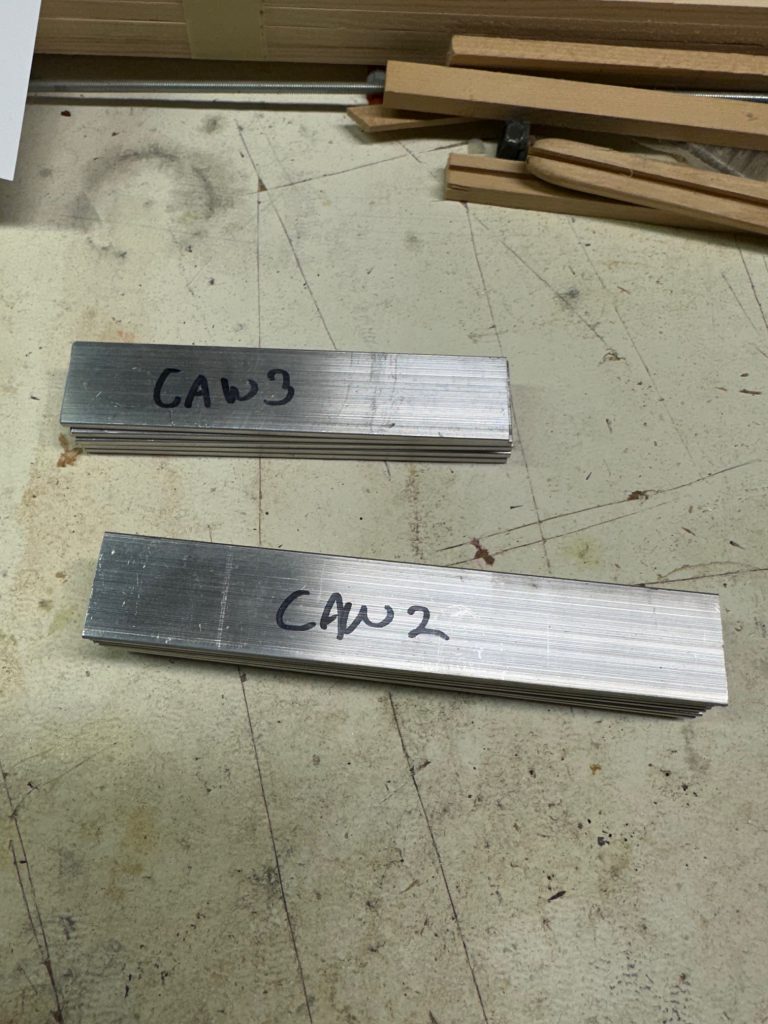
11/5/23 updates
Went over this morning to see what remaining tasks I could knock out before starting the first wing assembly, and to do some planning and figuring stuff out — like, how I was going to jig up the trailing edge and other stuff for the wings. Stu came in and had a fantastic idea for using the existing steel rails on his workbench to hold the TE flat and perfectly straight, then supporting the front of the ribs with the other rail. It’s a 10′ bench with 12′ rails, so plenty big enough. It’s a significantly different method than that suggested in the plans, but it’s a pretty unique setup. I’m sure a 2×4 shimmed for the correct angle is a lot easier solution for most people than adjustable 12′ long steel square tube rails. I’m just glad he had them built out of square tube and not round.
Next I gave the main and rear spars a once-over to make sure everything was right. It wasn’t. One of the upper wing main spar tip bow supports was off by 1/2″, the result of not having the two spars oriented the same way when I installed those parts. Or, maybe it was something else. Those supports have been a real pain in the rump, and I have a sneaking feeling I’ll run into issues there again. Anyway, the easiest fix was to cut the offending tip support off with a razor saw, put a slight angle cut on the root end, and re-attach it with appropriate splices. Right now part of the re-assembly is drying; I’m hoping to complete the assembly tonight after the epoxy cures.
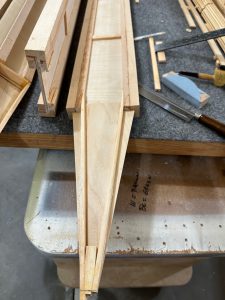
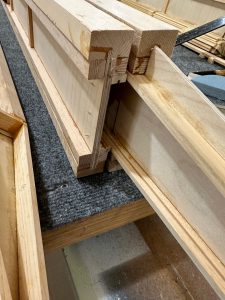
I got the ten ribs that I have over there trimmed fore and aft, so they’re ready for assembly. I’m planning to start with the lower left wing, just for the sake of simplicity. The lower right wing gets the wing walk. The two upper wings may or may not get fuel tanks, so I’ll do the lower wings first while I work that out. Therefore the lower left is the simplest and a good place to start, I think.
Stu and I discussed building the wingtip bows. He’s got a 48″ square table with a melamine top. It’s big enough to lay our two bows. I’ll wax it thoroughly and use a glue roller for gluing up the lamination strips. This will be good practice for the tail surfaces, which will need to wait until after the wings are done as they’ll need a 4 x 8 work surface. Now I just need to order a glue roller and about 40 or 50 more spring clamps. Given the size of the stabilizer & elevator assembly, more is better… I’m pretty sure there is no such thing as too many clamps.