Today I located and temporarily screwed the bearing blocks in, and cut the aileron free from the wing.
With that done, I decided to have another look at the wing walk situation. I don’t know why the support bits were the way they were, but I decided to just get on with making them work. When I look at the plans, especially the oblique view, indicate that the parts may have been cut in an attempt to match a much earlier version of the wing without much of the reinforcement at the main spar root. Anyway… Two of them had the aft end cut well enough to work at the rear spar. The inboard support needed to be trimmed at both ends. All had to be modified to fit the main spar.
In the end I got all three to fit, though I’m not terribly thrilled with the lack of good options for supporting and blocking the ends.
Next up were the notches for the cross braces. Most were too shallow and look to have been cut out with an end mill or router; the corners were rounded. I used a file to square up the corners and deepen the notches to fit the 1/2 x 3/4 pieces.
I figure I’ve got another hour or so of work to get all of the blocking and support in place before mixing epoxy. Probably more; I still haven’t figured out what I’m going to do about the extension of the walk forward of the main spar. If I build it to plans I’ll need to remove or hack up the first false rib. And of course the plywood pieces require significant modification.
On the bright side, the plywood skin for the wing walk curves nicely and won’t be a problem to get glued down. I’d been worried about that, and had visions of needing to make my own laminated piece there, but it’s fine.
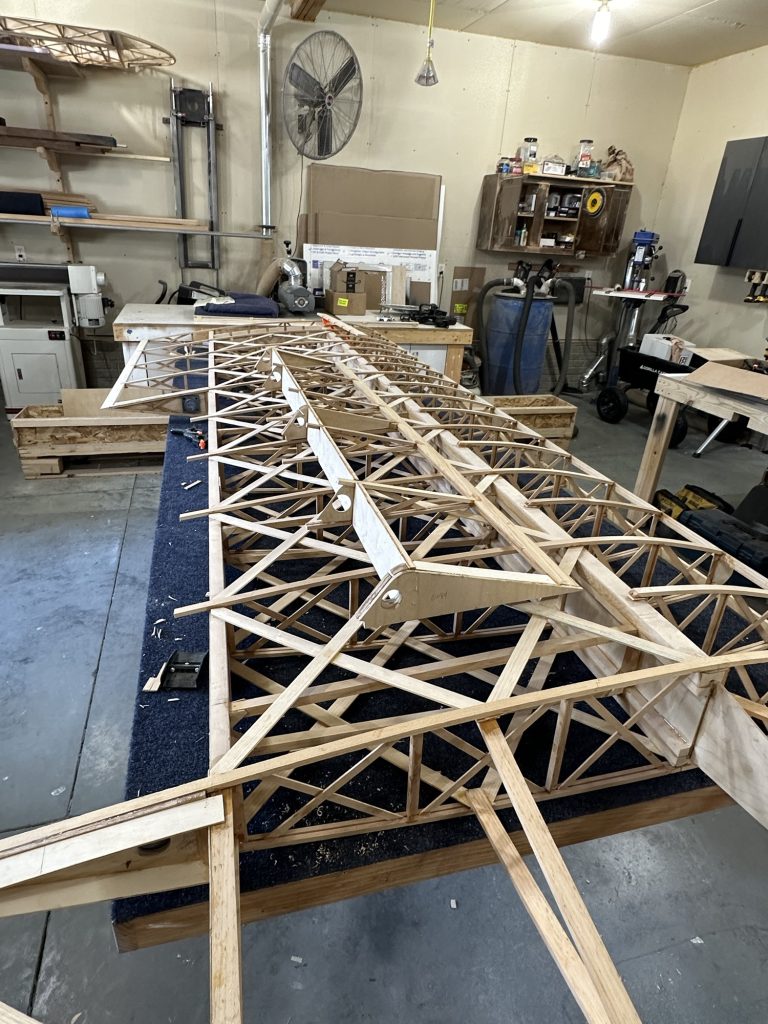

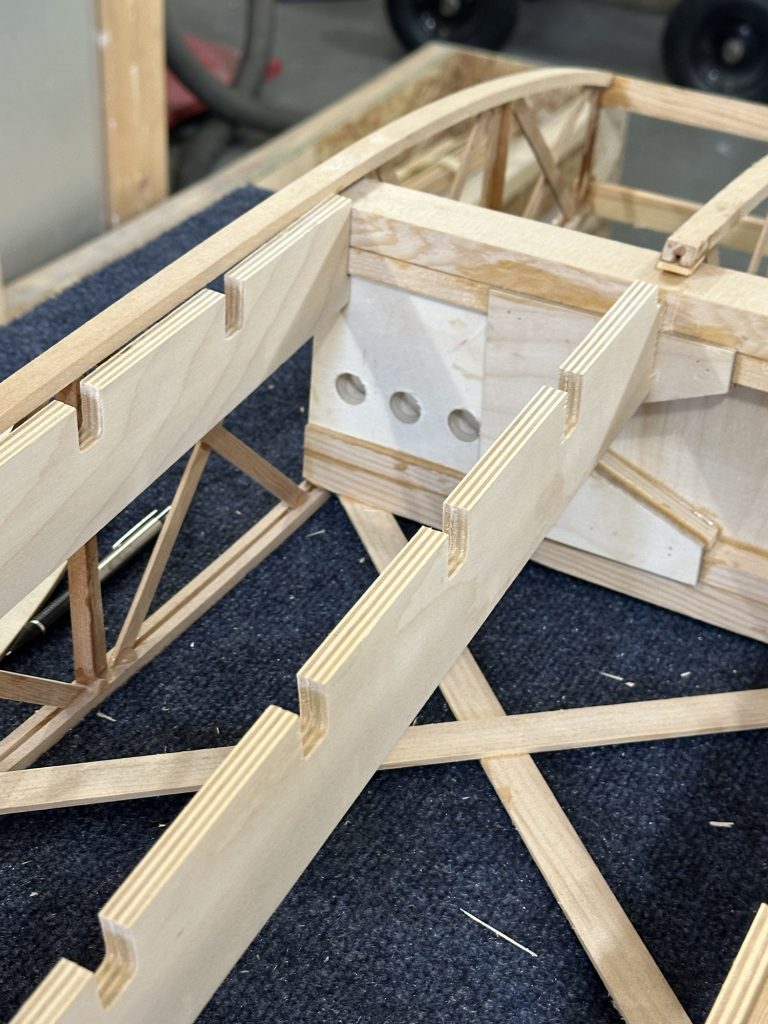
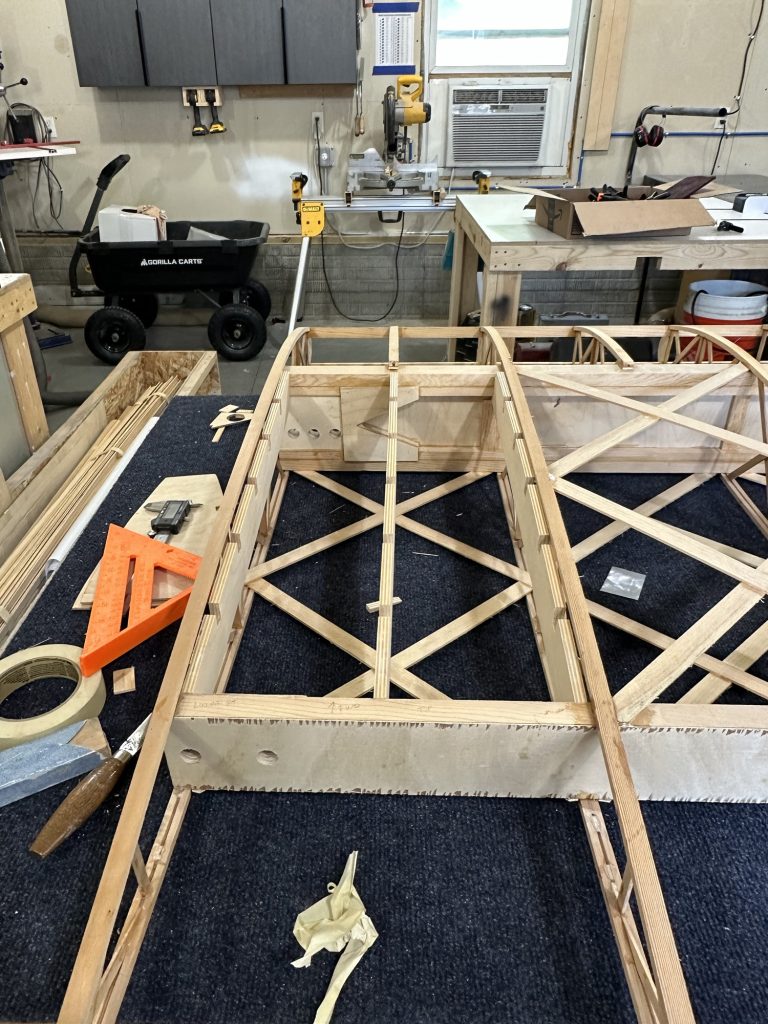
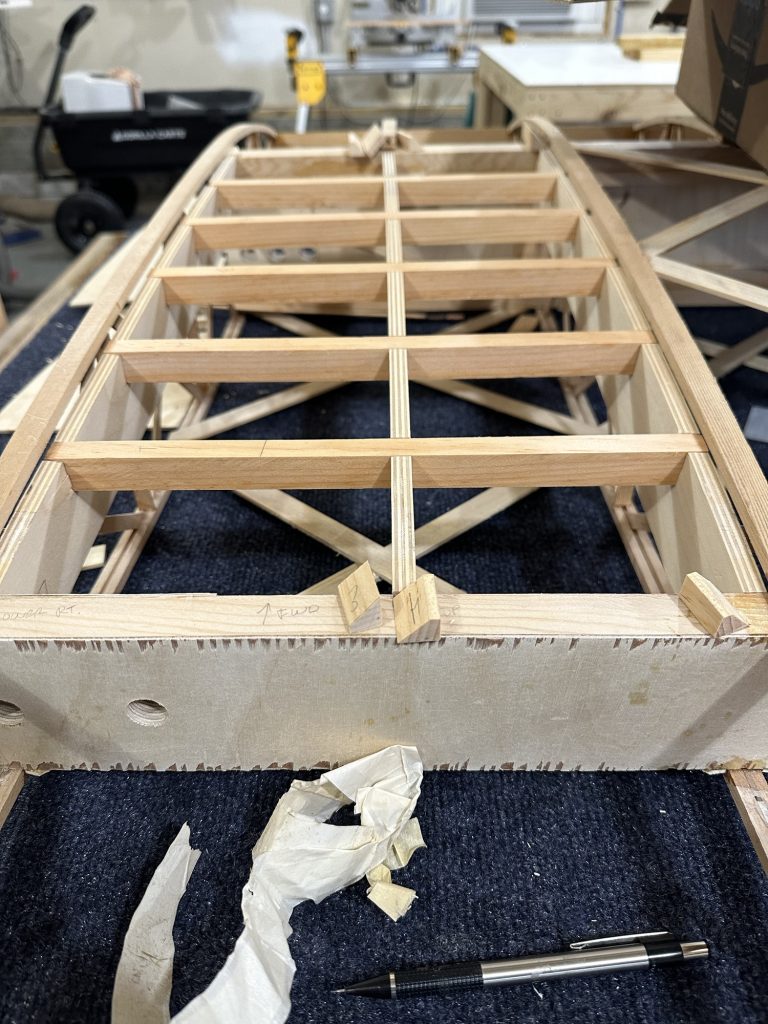